Textile Printing 101
- A+ Tutors Lanka
- Sep 13, 2020
- 6 min read
Updated: Oct 17, 2020
This article is just a brief summary of textile printing. It explains the types dyes and chemical additives used when dyeing different types of fabric.

Chemistry of Dyes
- Dyes have several chemical properties that enable to show color:
o They have chromophore groups which are responsible for color absorption. They absorb light in the 400 to 700 nm.
o They have resonance structures.
o They have a conjugated system where there is an alternation of double and single bonds.
- If the dye loses any one of these features the dye loses it color.
- Most dyes also contain auxochromes which are color helpers. These increase the λmax and εmax by extending the conjugation through resonance. It is an electron donating group. In other words, they regulate the intensity of color. They can also make dyes water soluble.
Ex: -NH2, -OH, -OR
- Chromophores are usually electron withdrawing groups.
- Chromophores and auxochromes are collectively known as chromogen.
- Mordent dyes are basic dyes that are reacted with a metal salt.
- Basic dyes are used to dye acrylic and can also be used to dye wool and silk.

Discharge Dyes and Printing
- Type of printing where a discharge ink is used to deactivate the dye on dyed fabrics.
- The discharge ink is clear with
an activator added to it.
- The activator is usually a type of formaldehyde sulfoxylate.
- In certain cases, water based pigments can be added to the discharge ink to get a different color on the area where the dye is deactivated.
- Process steps
o Preparation of fabric to be printed.
o Dyeing of fabric with dischargeable dyes.
o Preparation of discharge paste.
o Printing the discharge paste onto dyed fabric.
o Drying.
o Steam under atm condition or higher.
o Washing and soaping if required.
o Drying, finishing and packing.
- Discharge ability scale ranges from 1 to 5:
o 5 or 4-5 is suitable for white discharge.
o 4 or 3-4 is suitable for colored discharge.
o 1 is virtually un-dischargeable.
- Dyes suitable for discharge printing usually contain azo groups which can be split by reduction.
- Anthraquinone is a chemical catalyst that can be used to speed up the process.
- Leucotropes are substances used to improve whiteness in areas of fabric that have been discharged.
- Humectants improve penetration during steaming. Water attractor. Keeps fabric damp long enough for reaction to occur.
- Urea helps to dissolve more dye in each volume and it also acts as a humectant.
Acid Dyes and Printing
- Cannot be used with polyesters, polymers or cellulosic fibers.
- These are anionic dyes that do not work with polyester, cationic polymers or cellulosic fibers.
- These dyes can be used to dye protein fibers like wool, alpaca, silk, mohair, feathers and nylon which is chemically like silk.
- Acid dyes bond onto the fabric through hydrogen bonding, ionic bonding and van der Waals.
- They have SO3H groups that bond to the amino groups that are within the fibers.
- Structure of acid dye molecules
o Azo
o Anthraquinone
o Premetallized
o Triphenylmethane
- There are two types of premetallized:
o 1:1 where each dye molecule is complexed with a single metal atom
o 1:2 where each dye molecule is complexed with two metal atoms.
Disperse Dyes and Printing
- In 1924 Baddiley and Ellis produced the Sulpho Ricinoleic Acid (SRA) to dye acetate fibers. It was initially used as dispersing agent before they realized it can be used to dye hydrophobic fibers. In 1953 this dye was categorized as disperse dye.
- These dyes have been developed for dyeing polyester.
- The negative charge on the surface of polyesters cannot be reduced. Therefore, using non-ionic dyes is a necessity that is accomplished by using disperse dyes.
- Slightly water-soluble dyes that can be used to dye acetate (woven from wood pulp).
- They are usually applied from fine aqueous suspensions.
- These are widely used to dye a range of manufactured fibers.
- They are free from ionizing groups and are suitable for dyeing hydrophobic fibers like:
o Nylon, Polyester, Acetate, acrylic and other synthetic fibers.
- They have the smallest particle sizes among the different types of dyes.
- In the presence of nitrous oxide some shades of disperse dyes will fade.
- They don’t undergo any chemical change during dying.
- Good light fastness (4 to 5), moderate wash fastness (3 to 4).
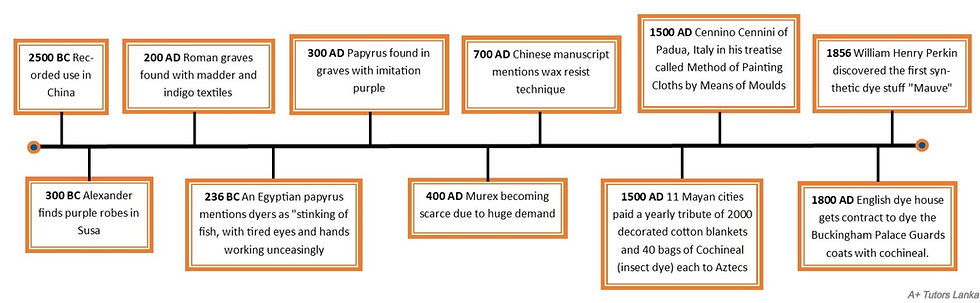
Vat and Sulphur Dyes
- Used on cellulosic fibers.
- The best option to obtain a fabric with the highest degree of fastness to industrial laundering, weathering and light.
- They are insoluble in water and cannot be applied directly.
- Sodium dithionite is used to first reduce the dyes. Then the fabric is reduced with this dye and hung to air dry.
- Or else the fabric is treated with oxidants such as potassium dichromate and acetic acid.
- This oxidizes the colorless compound into a colored dye which is now bound to the fabric.
Pigment Dyes and Printing
- Pigment dyes have large particle sizes and due to their insolubility in water and other organic solvents, they can be used to dye hydrophobic materials.
- Steps:
o Cationic pretreat is added to the fabric.
o Anionic dispersing agent is added to the pigment paste which consists of large colloidal particles as stated above.
o Then the pigment is exhausted onto the fabric.
o Process is completed by using a cationic binder to seal in the pigment.
Reactive Dyes
- Highly colored organic substances
- Used for dyeing cotton and other cellulosic fibers
- Can also be used on polyamides, wool, silk and acetate
- Forms a covalent bond with the dye molecule and fiber
- Has good fastness properties
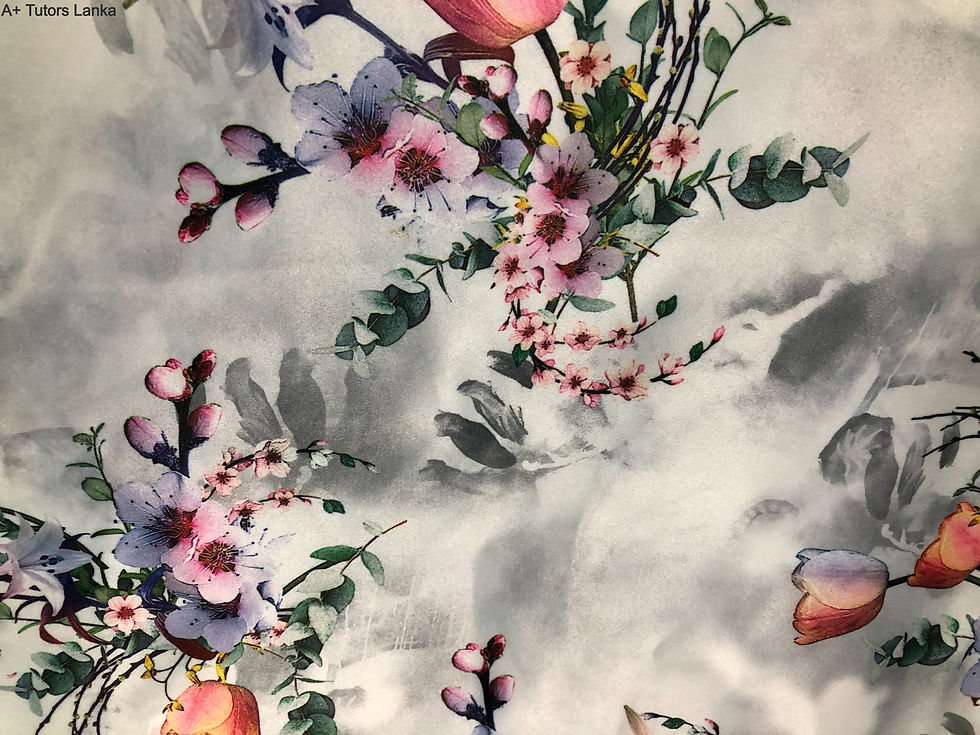
Digital Printing
- Digital textile printing is growing globally
- Expected to grow up to 1.4 billion m2 in this year
- Reduced substrate inventory
- Lower water and power consumption
- Unlimited number of colors
- Mass customization
- Fabric needs to be pretreated before printing to prevent excess ink penetration

Comparison of different types of printing (Extracted from Xingyu Li and Nancy Powell presentation)
Cellulosic Polymers
- Cotton, rayon, cellophane, linen and paper are examples of cellulosic polymers.
- They are hydrophilic and require hydrophilic dyes.
- Dyes designed for cellulosic fibers are direct, azoic, vat, Sulphur and reactive dyes.
- They have low wet fastness.
- To improve wet fastness, water insoluble dyes can be applied by using specific methods.
pH Effects on Dyes
- Lower pH in acid helps to form the hydrogen bonds between OH groups and amino acids.
- Silk can be dyed at high or low pH.
- Wool can only be dyed at low pH.
- Cellulose cannot be dyed at low pH.
Chemical Additives Used in Mother Dye Preparation
- Lyoprint is used as an anti-aerating and antifoaming agent
- Lyogen is used as a color yield improver for printing on polyester, wool, polyamide and cellulose.
- Lyocol is used as a highly effective solvent.
- Ammonium Sulphate used when applying acid dyes to wool or silk and is an acid donor.
o It is a fixating agent which is better than acetic acid.
o Unlike acetic acid, ammonium Sulphate does not boil off when steamed; therefore, gives better colors.
- Crosslinkers can be used under alkaline conditions to generate covalent bonds between cellulose and dyes containing nucleophilic groups. It is a process of joining polymers together.
o They produce several positive ions.
o They give strong prints on cotton and regenerated cellulose fiber.
o It results in good fastness properties.
- Polyprint is an anionic co-polymer thickener
- Periform is an anti-forming agent
- Rhodamine is a red dye that leaves a red color in water. It cannot be treated for easily but does not have extremely toxic properties. Completely removing the red color from water contaminated with rhodamine is extremely difficult which is why its release into rivers and streams is cautiously monitored here. Other than that, it is not extremely toxic to health.

Finishing
- Soda Ash or Sodium carbonate is used in the washing process to increase pH of the fabric.
- Citric acid can also be used to increase pH.
- pH of itching fabric
- Thermic Heater
- Acid and disperse dyes are steamed and washed.
- Pigment fabric not washed because steaming process infuses the binder into the dye and fabric; therefore, washing is unnecessary.
- Stenter
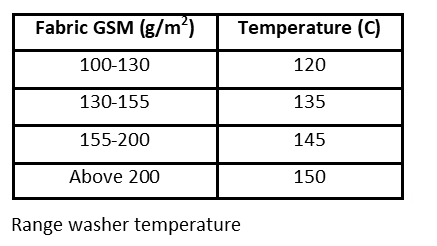
As you can see, dyeing a piece of fabric is not something that is straight forward. A lot of chemistry, experimentation and engineering goes into printing on fabric. By choosing the right type of dye on the right type of fabric, the textile industry produces beautiful and colorful designs that last even after years of use.
Hope you learned something new!
Comments